Underlayment Repair in Nashville, TN
Our professional underlayment repair service can save you thousands of dollars while extending the life of your existing floors. Many homeowners don't realize that flooring can often be repaired rather than replaced. Since 1779, Nashville has seen countless homes built, and many of these buildings now face flooring issues due to aging underlayment. We understand the unique challenges that come with Nashville homes, from historic properties downtown to newer constructions in the metropolitan area.
We take pride in our detailed approach to underlayment repair. When you contact us, we'll assess the condition of your floor structure, identify problem areas, and develop a targeted repair plan. Our team has the expertise to handle various underlayment materials, including plywood, cement board, and foam. You don't have to live with squeaky, uneven floors that diminish your home's comfort and value—we're here to provide a lasting solution that fits your needs and budget.
Types of Underlayment Materials
Underlayment is the crucial foundation layer that sits between your subfloor and finished flooring. We offer repair services for various types of underlayment materials, each with specific advantages for different flooring applications.
Plywood and OSB Underlayment
Plywood underlayment is one of the most common materials we repair and replace. It provides excellent stability and structural support for many flooring types. When your plywood underlayment shows signs of water damage, warping, or delamination, we can restore it to its original condition.
OSB (Oriented Strand Board) underlayment is a cost-effective alternative to plywood that we also frequently service. OSB repair requires special attention as this material can swell more dramatically when exposed to moisture.
Our team has expertise in identifying areas of OSB that need replacement versus areas that can be salvaged through proper drying and treatment. Both materials typically last 20-25 years when properly installed, but environmental factors can shorten this lifespan.
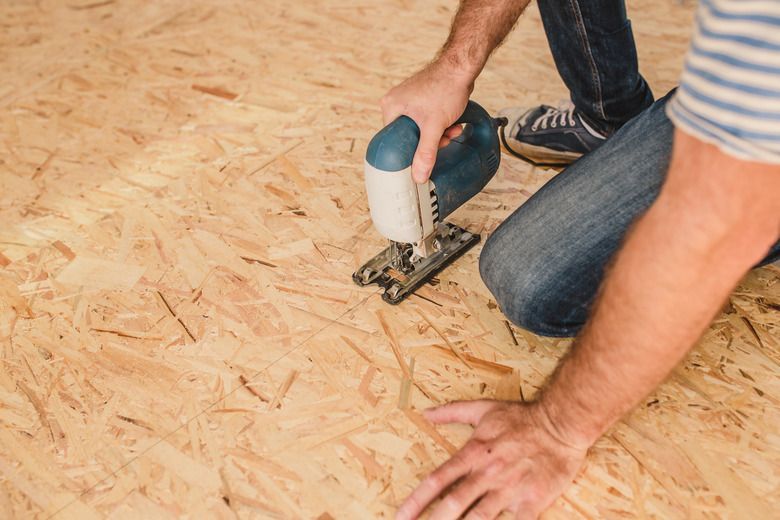
Concrete and Asphalt Underlayment
Concrete underlayment repairs are among our specialties at Nashville Flooring Company. We address common issues like cracks, uneven surfaces, and moisture problems that can compromise your flooring.
Our concrete underlayment restoration includes leveling compounds to create the perfect base for your new flooring. This step is crucial for preventing future issues with tile, vinyl, or hardwood installations.
Asphalt underlayment, though less common in residential settings, requires specialized repair techniques. We handle asphalt underlayment repair with expertise, addressing issues like crumbling, cracking, or separation that can occur in commercial applications. Our team uses industry-approved methods to ensure your asphalt underlayment provides a stable foundation.
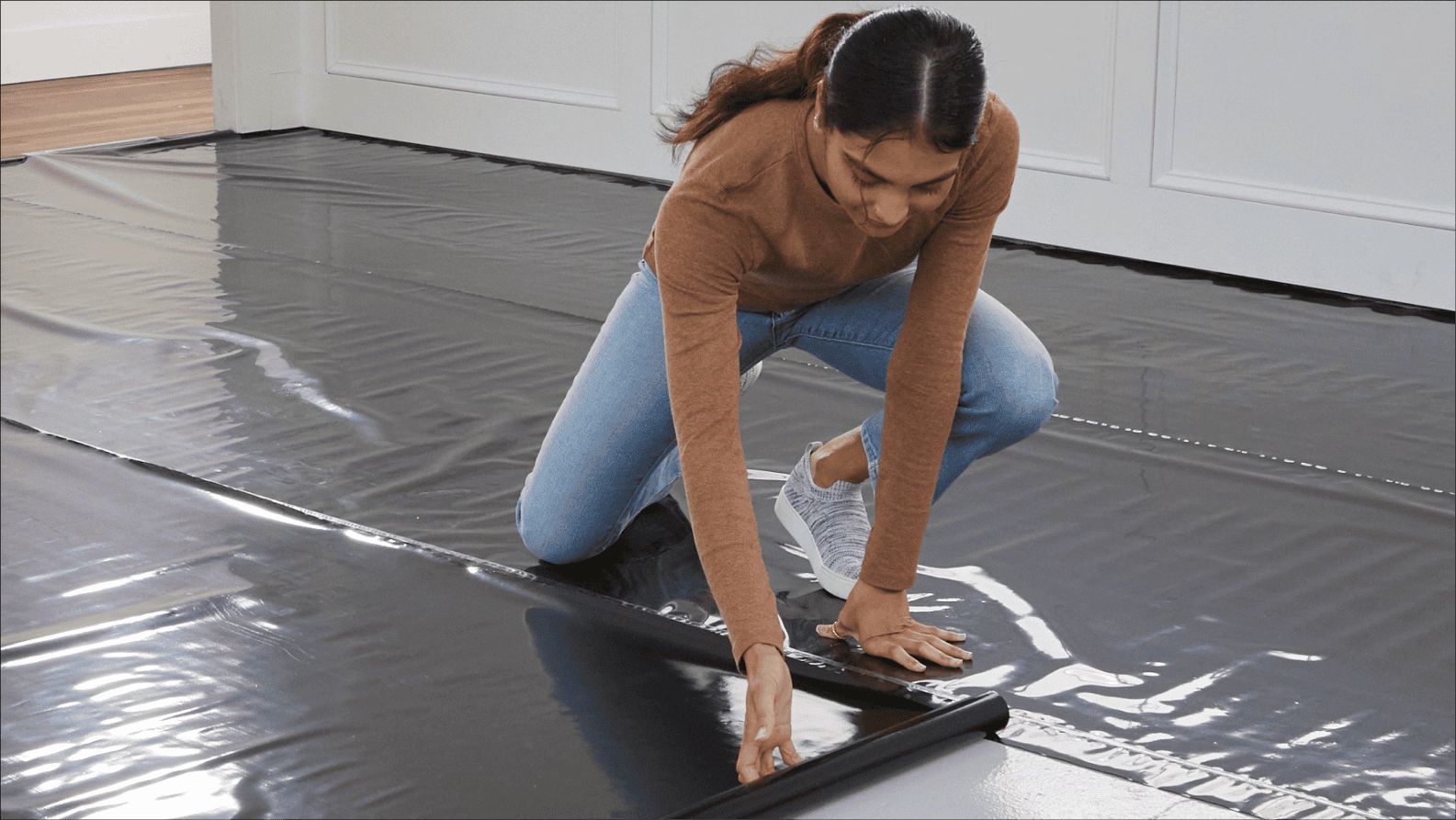
Felt underlayment replacement is a common service we provide, especially for roofing and some flooring applications. This material offers good moisture protection but can deteriorate over time.
When your felt underlayment shows signs of mold, moisture damage, or deterioration, our team can quickly replace it to protect your flooring investment. We use premium-grade materials that offer superior moisture resistance.
Peel-and-stick underlayment is popular for DIY projects, but professional repair is often needed when installation problems arise. Our repair services address adhesion failures, bubbling, and moisture infiltration issues. We can fix poorly installed sections or replace the entire underlayment if necessary.
Felt and Peel-and-Stick Underlayment
Specialty Underlayment for Soundproofing and Thermal Management
Soundproof underlayment repair requires technical expertise to maintain acoustic properties. Our team specializes in restoring cork, rubber, and foam-based sound-dampening underlayments without compromising their noise-reduction capabilities.
We can repair or replace your soundproofing underlayment to maintain peace between floors. Our solutions meet building code requirements for sound transmission.
Thermal underlayment helps improve your floor's energy efficiency. When your thermal underlayment sustains damage, we can restore its insulating properties. We work with various materials including cork, felt-rubber composites, and specialized foam designed to create temperature barriers.
These specialty underlayments typically combine different materials to provide multiple benefits beyond basic cushioning, including moisture protection and thermal regulation.
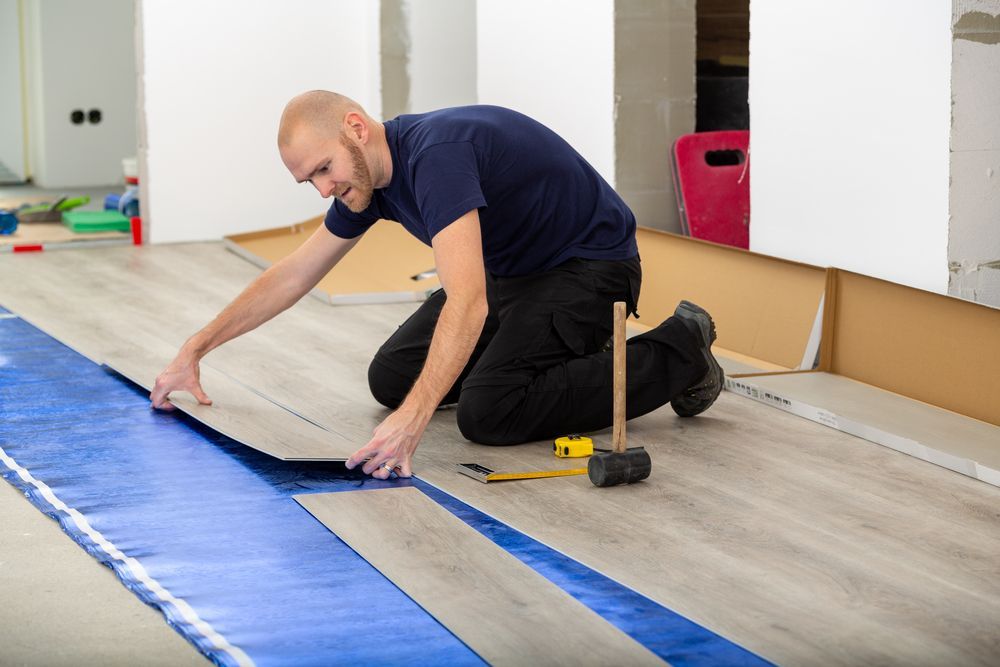
Common Underlayment Problems and Diagnosis
Identifying underlayment issues early can save you time, money, and prevent more serious flooring failures. Underlayment problems often show specific warning signs that help pinpoint the exact issue requiring attention.
Moisture Damage and Water Intrusion
Moisture is the number one enemy of floor underlayment. You might notice musty odors or discoloration as early warning signs of water damage. Soft or spongy spots when walking across your floor often indicate underlayment that has absorbed moisture and begun to deteriorate.
We use moisture meters to accurately detect dampness levels in underlayment materials. For concrete subfloors, we perform calcium chloride tests to measure moisture vapor emission rates before installing new underlayment. Prompt repair of plumbing leaks and proper waterproofing can prevent most moisture-related issues.
Cracks, Tears, and Punctures
Physical damage to underlayment manifests as visible cracks, tears, or punctures. These defects often develop when heavy items are dropped on the floor or when furniture with sharp edges is dragged across the surface.
We can often repair isolated tears or punctures without complete tear-out, saving you considerable expense. Our repair process involves careful cutting around the damaged section, removing the compromised material, and installing a properly sized replacement piece with appropriate adhesives.
Warping, Buckling, and Uneven Surfaces
Uneven floors with ridges, humps, or dips usually indicate underlayment that has warped or buckled. You might notice areas where the floor feels unstable underfoot or where furniture wobbles.
For minor ridges, we sometimes use specialized grinding equipment to level the surface. More severe buckling typically requires removing the affected sections and installing new underlayment. We always check for underlying structural issues that might have contributed to the problem.
Adhesive Failures and Bonding Issues
Poor surface preparation before installation is a common cause of bonding issues. Dust, debris, or existing adhesive residue prevents new adhesive from creating a proper bond. Incorrect adhesive selection for your specific underlayment type can also lead to premature failure.
We test adhesion strength in suspect areas using non-destructive techniques. Our repair options include injecting adhesive through small holes to rebond loose sections or removing and replacing areas with complete adhesive failure. We prepare surfaces thoroughly before applying new materials to ensure proper bonding.
Request Your Free Quote Today
Transform your home with sustainable flooring options today! Our eco-friendly flooring solutions are ready to bring beauty, durability, and environmental responsibility to your Nashville home.
Call us at (615) 555-7890 to schedule your free in-home consultation. Our flooring experts will bring samples directly to you, making it easy to visualize how each option will look in your space.
Request your free quote today! Complete our simple online form, and we'll respond within one business day with pricing options tailored to your specific needs.