Mezzanine Floor Construction in Nashville, TN
Our mezzanine solutions create valuable additional square footage without the need for costly expansions or relocations, effectively doubling your usable space while maintaining your current footprint.
We bring our flooring expertise to mezzanine construction, carefully selecting high-quality materials that match your specific needs. Our steel mezzanines offer exceptional strength and longevity, while our diverse flooring options include steel grating, wood, and composite materials. Each choice is tailored to your specific usage requirements, ensuring your new space functions perfectly for your business operations.
Serving Nashville and the greater Middle Tennessee area, we understand the unique challenges local businesses face when it comes to space optimization. Our appointment-based consultation process makes getting started simple - we'll assess your space, discuss your needs, and provide a comprehensive plan for your mezzanine construction. With over two million residents in the metropolitan area, we've helped countless businesses across diverse industries maximize their valuable commercial real estate through our professional mezzanine construction services.
Types of Mezzanine Floors
Steel mezzanine floors are our most popular option for industrial settings. They offer exceptional strength, durability, and moisture resistance while requiring minimal maintenance. These structures can support heavy loads and equipment, making them perfect for warehouses and manufacturing facilities.
Commercial mezzanines are designed with aesthetics and functionality in mind. We typically construct these with a combination of steel framing and attractive finishes to blend seamlessly with retail or office environments. These mezzanines often feature customized railings, stairs, and decking materials that complement the existing architecture.
Warehouse mezzanines maximize vertical storage space by creating additional levels for inventory. We can design these systems with specialized racking integration, conveyor accommodations, or designated picking areas to improve operational efficiency.
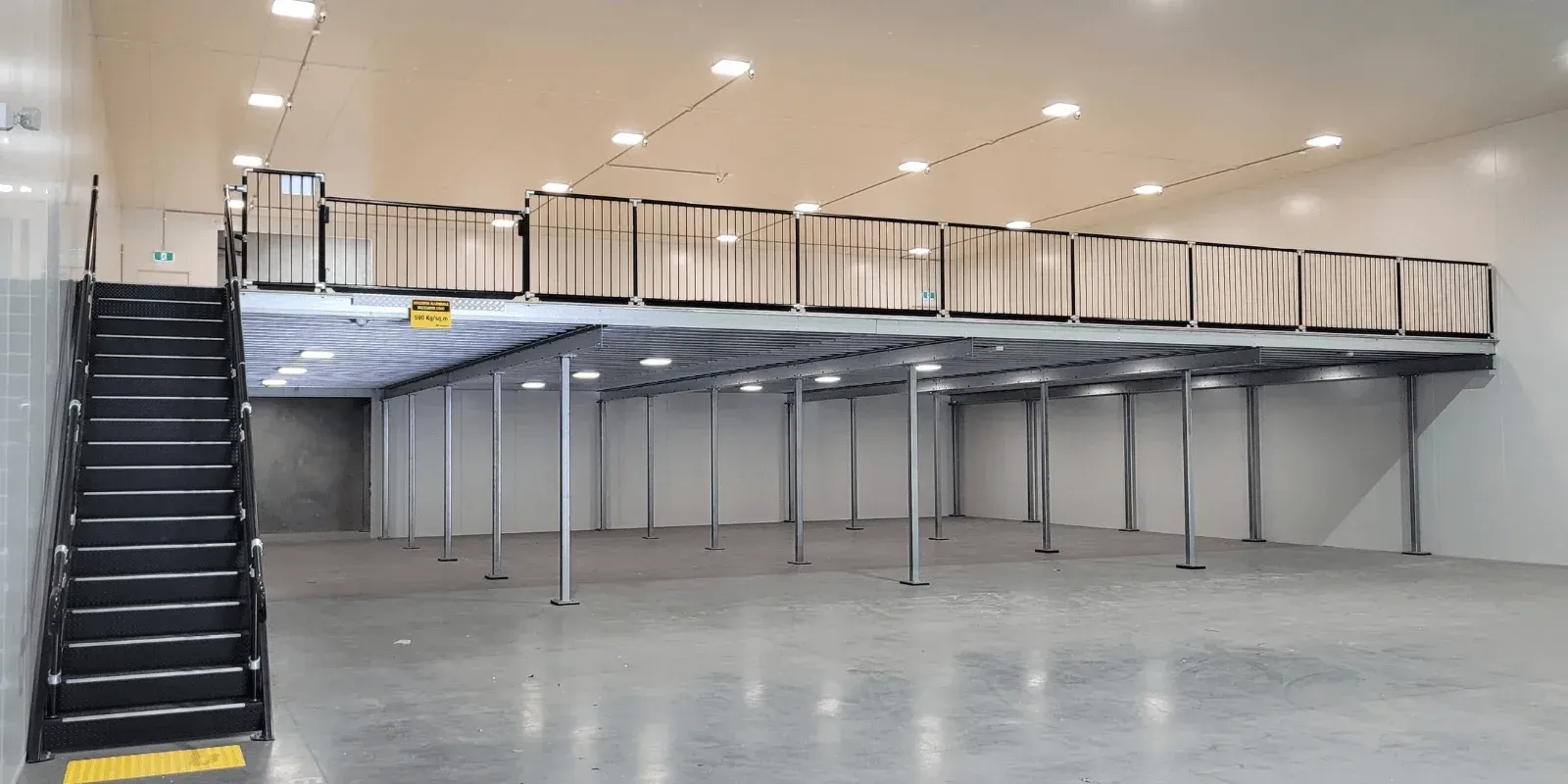
Benefits of Installing a Mezzanine Floor
Mezzanine solutions provide immediate space expansion without the costs of relocation or new construction. You can nearly double your usable square footage without increasing your property footprint or lease payments. This makes mezzanines one of the most cost-effective ways to solve space constraints.
Our mezzanine systems are fully customizable to meet your specific needs. We can design around existing structures, equipment, and workflow patterns to minimize disruption to your operations. The modular nature of our mezzanines also means you can reconfigure or expand them as your needs change.
Installation is typically much faster than traditional construction. You'll experience minimal downtime and can often continue operations during much of the installation process. Our mezzanines also don't usually require permits for permanent construction, saving you time and administrative hassle.
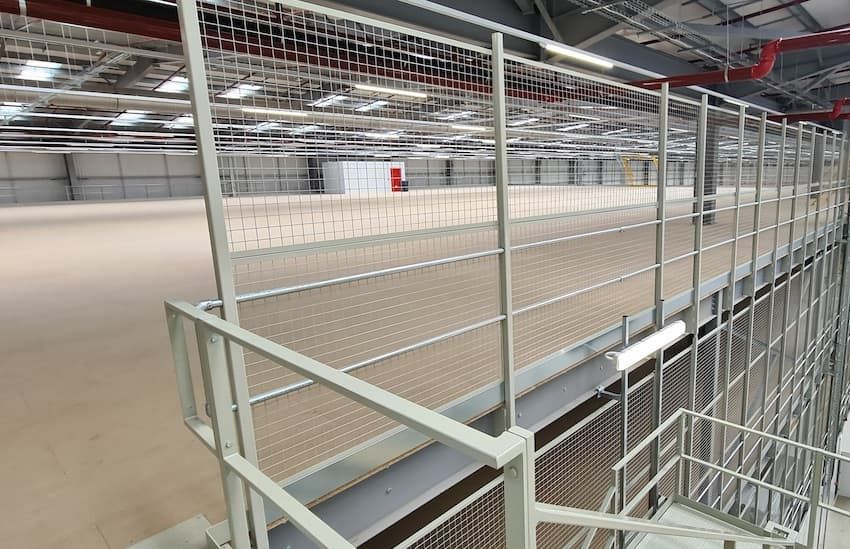
Our Mezzanine Floor Construction Process
This is the text area for this paragraph. To change it, simply click and start typing.
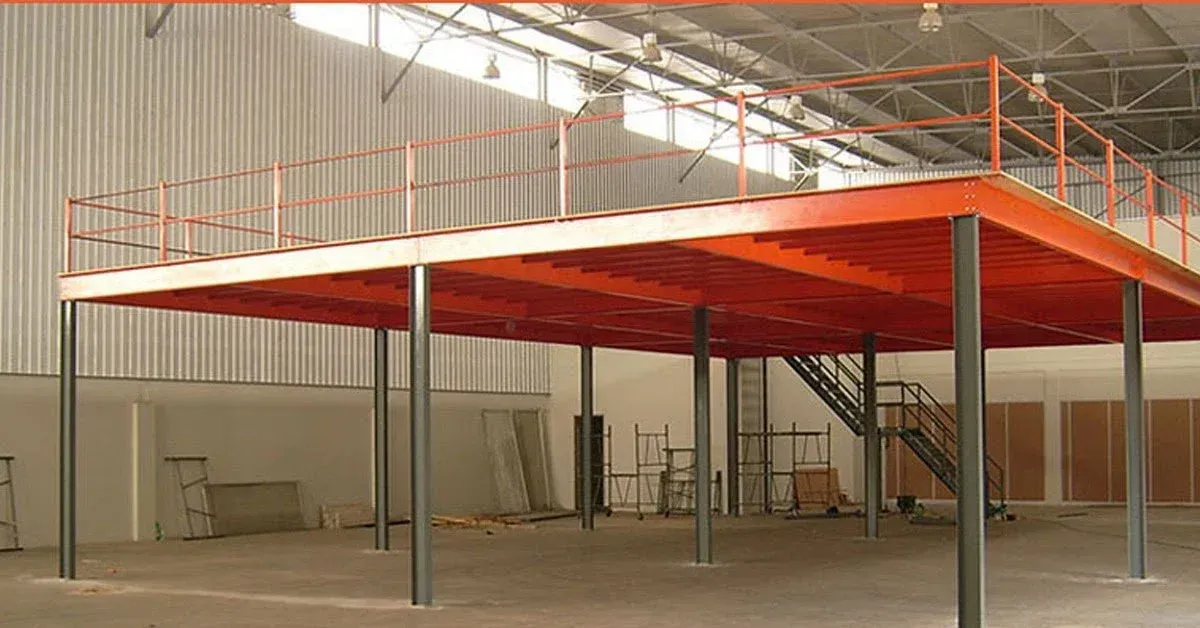
1. Pre-construction and Planning
We begin every mezzanine floor project with a thorough site analysis to understand your space's unique characteristics. Our team visits your location to take precise measurements and identify any potential obstacles like columns, electrical fixtures, or plumbing that might affect the design. We examine ceiling heights to determine maximum mezzanine height potential and evaluate floor conditions to ensure proper support.
During this phase, we also assess access points for material delivery and installation equipment. We'll work with you to develop a timeline that minimizes disruption to your operations. Our site analysis includes checking building codes and local regulations to ensure compliance from the start.
Your existing floor's load-bearing capacity is carefully evaluated, as this will influence the mezzanine design and support requirements. We document everything with detailed photos and measurements to guide our planning process.
2. Engineering Calculations and Load Assessments
Our mezzanine engineers conduct comprehensive load assessments to determine the weight requirements for your specific needs. We calculate both dead loads (the structure itself) and live loads (people, equipment, and materials that will occupy the space). These calculations are crucial for developing a safe, code-compliant mezzanine system.
We use advanced software to model structural behavior under various conditions, ensuring your mezzanine can handle intended uses safely. Our engineering team creates detailed specifications for all structural components, including columns, beams, and decking materials.
The mezzanine floor plan is developed based on these calculations, with precise dimensions and component placements marked. We provide clear documentation of all engineering calculations for permit applications and your records. Safety factors are built into every calculation to ensure long-term structural integrity beyond minimum requirements.
Our mezzanine consultants work directly with you to optimize the design based on both technical requirements and your operational needs.
3. Selecting Appropriate Materials and Finishes
We carefully choose materials based on your specific needs and applications. For industrial settings, we typically recommend steel structural components that provide superior load-bearing capacity and durability. Our steel mezzanines can support weights from 125 to 300 pounds per square foot, depending on your requirements.
For flooring surfaces, we offer several options including B-deck with concrete, resin-sealed plywood, or diamond plate steel. Each material has distinct advantages based on your usage. Open grating works well for ventilation needs, while solid surfaces provide better noise reduction.
Railings and stairs are constructed to meet all safety codes while complementing your space. We can match existing color schemes and finishes to create a cohesive look. Our powder-coated finishes resist chipping and corrosion, extending the life of your mezzanine structure.
4. Cost-Efficient Construction Methods
We employ modular construction techniques that significantly reduce installation time and labor costs. Our pre-fabricated components arrive ready to assemble, minimizing disruption to your operations. This approach typically saves 30-40% compared to traditional construction methods.
Our bolt-together designs eliminate the need for welding on-site, creating a cleaner installation process. This method also allows for future modifications or relocation if your needs change.
We use precise computer-aided design to optimize material usage and eliminate waste. Before construction begins, we conduct thorough site evaluations to identify potential challenges and develop solutions in advance.
For many projects, we can integrate your mezzanine with existing structures, saving on materials and maximizing usable space. Our column layouts are strategically planned to minimize interference with ground-level operations while ensuring structural integrity.
5. Finishing Touches and Ancillary Elements
The final details of your mezzanine floor installation can dramatically impact both functionality and appearance. These finishing elements transform a basic structural addition into a seamless part of your facility that works perfectly for your specific needs.
At Nashville Flooring Company, we offer a variety of railing options to complement your mezzanine design concept. Our standard safety railings come in powder-coated steel with options for custom colors to match your existing décor.
For more upscale environments, we provide stainless steel and glass balustrade systems that create a modern, open feel while maintaining required safety standards. These premium options work exceptionally well in retail or office environments where appearance matters.
Every railing we install meets OSHA requirements for height and load capacity. We can incorporate kickplates, mid-rails, and custom gate access points based on your specific workflow needs and safety concerns.
6. Optimizing Lighting, Ventilation, and Insulation
Proper lighting transforms a mezzanine from a basic storage platform into a fully functional workspace. We install recessed LED fixtures that provide abundant light without reducing headroom. Task lighting can be added in specific work areas to increase visibility.
Ventilation needs vary based on your mezzanine's purpose. For enclosed spaces, we can integrate with your existing HVAC system or install dedicated ventilation to ensure comfortable working conditions year-round.
Insulation options include spray foam or rigid panel systems for temperature and sound control. This is particularly important if your mezzanine will house noise-sensitive operations or require specific climate conditions.
We also pay close attention to electrical needs, installing appropriate outlets, data ports, and specialized connections based on your equipment requirements.
7. Maintenance Guidelines and Longevity
We recommend conducting regular inspections of your mezzanine floor at least twice a year. Check for any loose connections, signs of wear, or damage to railings and staircases. Keep the surface clean by sweeping regularly and promptly addressing spills to prevent potential slipping hazards or material deterioration.
For steel mezzanines, inspect for rust or corrosion, especially in high-humidity environments. We suggest applying protective coatings every 3-5 years depending on usage conditions.
Weight distribution remains important even after installation. Avoid exceeding the designed load capacity and distribute heavy items evenly across the floor. This prevents unnecessary stress on specific areas of the structure.
Keep all access points clear of obstructions and maintain proper lighting around stairs and edges. We provide detailed maintenance manuals tailored to your specific mezzanine design when we complete the installation.
Key Structural Components of a Mezzanine
A well-designed mezzanine floor relies on several critical structural elements that work together to ensure safety, stability, and functionality. Each component plays a vital role in supporting the intended load while maintaining compliance with building regulations.
Expertise in Eco-Friendly Flooring
Local Nashville Knowledge
Support Columns and Mezzanine Beam Layout
Our structural mezzanines are built on a foundation of strategically placed support columns that transfer the load to the building's floor. We typically use steel columns for optimal strength-to-weight ratio, placing them at calculated intervals based on your specific load requirements. The columns connect to a network of primary and secondary beams that form the skeleton of your mezzanine structure.
The beam layout is crucial for distributing weight evenly across the entire structure. Our engineers design beam configurations that maximize open space below while ensuring adequate support above. For heavier applications like storage or manufacturing, we install beams with deeper profiles and closer spacing. We calculate your specific mezzanine load capacity during the planning phase to ensure the column and beam system exceeds your operational needs.
Integration of Mezzanine Decking and Flooring
The decking system forms the actual usable surface of your mezzanine and must be selected carefully based on your intended use. We offer several decking options including steel plate, bar grating, and various wood composites. Each material provides different benefits regarding fire resistance, sound dampening, and aesthetic appeal.
For standard applications, we often recommend tongue-and-groove particle board covered with hard-wearing vinyl or carpet depending on your needs. In industrial settings, we might suggest steel decking with a concrete overlay for maximum durability and fire resistance. The connection between the decking and beam structure is engineered to prevent unwanted movement and vibration. This integration ensures your mezzanine feels solid underfoot while maintaining its structural integrity over years of use.
Benefits of Organic Floor Coverings
Organic floor coverings offer significant advantages beyond their eco-friendly credentials. These natural flooring solutions provide tangible benefits for your home environment, financial outlook, and personal wellbeing.
Enhanced Indoor Air Quality
Conventional flooring materials often emit volatile organic compounds (VOCs) that contaminate your indoor air. These harmful chemicals can persist for years after installation, leading to respiratory issues and allergic reactions.
Organic floor coverings are manufactured without these toxic compounds. Natural materials like cork, bamboo, and wool carpeting don't release harmful gases into your home.
Long-Term Cost Savings
While organic flooring may require a higher initial investment, the long-term financial benefits are substantial. Natural materials typically outlast conventional alternatives by decades when properly maintained.
Hardwood floors from sustainable sources can last 100+ years, compared to vinyl's 10-20 year lifespan. This durability eliminates the need for frequent replacements.
Eco-Conscious Home Value
Homes with organic flooring installations typically command higher resale values in the Nashville market. Modern homebuyers increasingly prioritize sustainable features when making purchasing decisions.
Real estate professionals report that eco-friendly flooring can increase property valuation by 3-5%. This premium stems from both aesthetic appeal and perceived health benefits.
Health & Comfort Advantages
Organic floor coverings create naturally comfortable living spaces. Cork and wool provide cushioning underfoot, reducing joint stress and fatigue during extended standing periods.
These materials offer excellent thermal properties, maintaining comfortable temperatures year-round. In Nashville's hot summers, organic flooring stays naturally cool to the touch.
Request Your Free Quote Today
Transform your home with sustainable flooring options today! Our eco-friendly flooring solutions are ready to bring beauty, durability, and environmental responsibility to your Nashville home.
Call us at (615) 555-7890 to schedule your free in-home consultation. Our flooring experts will bring samples directly to you, making it easy to visualize how each option will look in your space.
Request your free quote today! Complete our simple online form, and we'll respond within one business day with pricing options tailored to your specific needs.